Home » Posts tagged 'ultrasonic welding'
Tag Archives: ultrasonic welding
The Different Types of Plastic Molds Used in Manufacturing Plastic Parts
The mold is a key component to making plastic parts. The quality of the mold, CNC machining, and processing are vital to the end product.
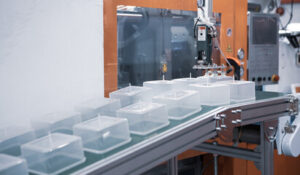
Family injection molds are great for smaller runs of the same product. They cut down on maintenance costs and material use by creating different variations of a single part in one mold. Read on American Plastic Molds for more information.
Extrusion molding involves squeezing hot, liquid raw plastic through a shaped hole called a die. The die, which is custom made for the desired result, determines the shape of the finished product. This process produces long, thin shapes such as tubes and rods. It is also ideal for producing molded sheets and films.
The raw material starts as pellets or granules that are stored in a hopper and fed into a heated barrel. The pellets or granules are melted into a thick liquid. This liquid is then forced through a die, taking on the shape of the die’s cross-section. The resulting workpiece is then cooled and solidified to its final form.
This process is used to make a variety of products, including pipes, hoses, drinking straws, curtain tracks and rods. It is especially useful for creating parts that have a fixed cross-sectional profile, such as those found in the plumbing industry. In some cases, this process is more cost-efficient than injection molding, particularly for long production runs.
The process is optimized by balancing material flow, cooling rates (for hot extrusions) and production speeds. This helps to ensure quality and reduce waste. In addition, by using the latest technology to control the process, producers can increase output while reducing energy consumption.
Injection molding uses a very high temperature in order to melt the raw material and then push it into a mold under pressure. This makes it ideal for making products that require high levels of strength and durability. It is also suitable for manufacturing large, hollow parts. For example, it can be used to produce tubing for cars or building materials that replace glass.
Injection molding allows for an unlimited number of design possibilities. It is also possible to add fillers to the liquid plastic, which increases its strength and allows for more color options. In addition, the process is highly automated and requires only a single operator to oversee it. This leads to lower start-up costs and reduced labor costs compared with other manufacturing methods. This also means that production can be done much faster, making it a popular choice for low-volume manufacturing.
Injection Moulding
Injection moulding is a versatile process that allows for high production speeds and the ability to make very complex parts with tight tolerances. It is also capable of producing parts with different materials in a single injection, which makes it ideal for multi-material products and parts that require assembly. It is also possible to incorporate features that would be impractical or impossible to produce using other techniques, such as bosses, ribs and metal inserts.
The process begins with pelletised raw material fed into a heated barrel via a screw. This increases the temperature, reduces the viscosity and homogenises the thermal energy distribution. Once the material is at the correct temperature, it is injected into the mould and quickly fills the cavity to a predetermined depth. The build-up of pressure packs and holds the material together as it cools. The result is a shaped, finished plastic part.
A standard two-plate mold will contain a core and a cavity. The core is an inner section that gives the part its shape, and the cavity is the hollow space within it. The shaped sections are known as gates, runners and sprues and help to guide the melted plastic through the process. The sprues are attached to the runner plates, which connect them to the gate. The sprues and runners allow air to escape during the cooling process, which helps prevent shrinkage and warping.
Once the molten plastic has been filled into the cavity, a hold pressure is applied until it is 95% solidified. This is about half of the injection pressure and helps to improve the compactness of the molded part, control cooling and shrinkage and reduce cycle times.
After the product has cooled, it is removed from the mold by the ejection unit. It is then inspected for defects such as flashing, where a thin layer of melted plastic appears on the surface. Any problems are then rectified before the next run of the product is produced. The whole process takes about 2 minutes from start to finish. Depending on the machine’s clamping pressure or tonnage, it is possible to produce millions of different products each year.
Rotary Moulding
A common plastic manufacturing technique, rotational molding (also known as roto-molding) uses a hollow mold that is filled with powdered resin and slowly rotated while being heated. The rotation allows the resin to evenly coat the walls of the mold and creates a strong, durable product. After a set amount of time, the mould is cooled and demoulded. This method is ideal for producing hollow, thin-walled products that require alignment of wall thickness and high stability.
One of the most significant benefits of rotomolding is its ability to provide a smooth finish on the finished product. Injection mold plastics have visible hems and seams, but rotomolding produces a smooth surface that can be easily decorated with textures or symbols. The smooth surface also makes roto-molded products easier to clean and disinfect.
Additionally, a rotomolding process can be a more economical choice for larger production runs than other manufacturing techniques. This is primarily because the process produces only one single part, removing the need for downstream processes such as trimming and stripping. This can reduce the cost of materials by as much as 40 percent. It can also result in less waste material in the form of runners and sprues.
Another advantage of rotomolding is its flexibility in terms of the size of the final product. It can produce plastics in sizes ranging from ping-pong balls to 21,000 gallon tanks. This means that roto-molding is ideal for large-scale production of custom products, including industrial containers and electrical enclosures.
Finally, rotomolding is an excellent choice for creating long-lasting products that can resist harsh environmental conditions. Its high-density material, such as polyethylene, protects against UV rays and prevents rust and corrosion. In addition, the rotomolding process can be used to add reinforcing ribs called kiss-offs to help improve the strength of the product.
These ribs are built into the product to distribute forces more evenly, allowing it to withstand greater stresses and still maintain a smooth finish. This can be a significant benefit for companies that manufacture items such as trash bins, residential carts, and chemical containers, which often need to endure heavy-duty use.
Pressure Moulding
Pressure molding is one of the most common methods for producing a wide variety of plastic parts. It uses high pressure to compress a thin layer of thermoplastic material to create a part. The process is typically used to produce large durable parts, such as car bumpers and door panels. It is also capable of creating smaller more intricate parts. This type of manufacturing is suited for high production runs and can easily handle millions of parts per machine per year.
The primary steps involved in the pressure molding process include:
This step is where you heat the materials to their molten state and then feed them into the mold cavities. The machine will then apply the required amount of pressure to the mold. After the part has been formed it will then need to cool and harden.
After the part has been cooled and hardened it will be removed from the mold. There may be some trimming and routing operations that need to be completed before the part can be fully integrated into the final product. These additional processes can be time consuming and expensive, but with proper planning many of these steps can be avoided.
A common problem encountered in injection molding is flow marks. These are visible lines on the surface of the finished part and result from the merging of separate melt flow fronts. The causes of these can include inadequate gate location and size, excessive injection pressure, or improper venting. These issues can be corrected by optimizing the number and location of gates, increasing melt and mold temperatures, and improving venting channels in the tool.
Another problem that can occur in injection molding is shrinkage. This is the tendency of the molded part to shrink after it has been formed. The main cause of this is uneven cooling and rapid solidification of the molded part. This can be corrected by ensuring uniform cooling across the part, and utilizing a properly designed mold.
Compression molding is a great choice for producing complex products like LED lighting, switch and sensor electronics, mobile batteries, camera modules, solar inverters, etc. It can also be used for smaller parts such as fender parts, dashboards, and motor housings. Compression molding is more cost effective than injection molding and allows for the use of lower grade aluminum material to maintain durability.